|
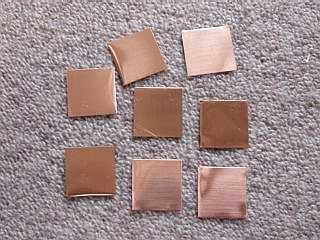 |
|
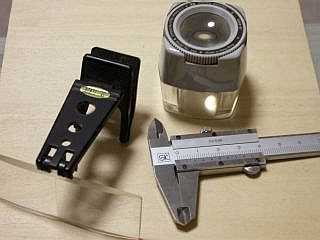 |
|
|
銅板は20-25mm角位に極力曲がらないよう切断します。 私はペーパーカッターで切断しましたが、ハサミで切る場合には曲がりやすくなります。
|
|
細かな工作の3種の神器。 左が両眼用ルーペ、手前はノギス、奥が高倍率ルーペです。
|
|
|
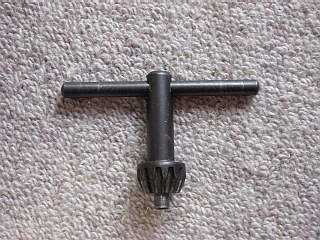 |
|
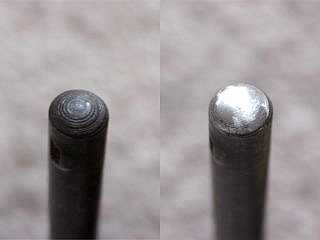 |
|
|
ドリルのチャック回しハンドルですが、この横棒の頭が丸いのを利用して、銅板に凹みをつけます。
|
|
左は元々の横棒端のクローズアップ。 かなり粗いのでヤスリで削りペーパーで研磨して右のようにしました。
|
|
|
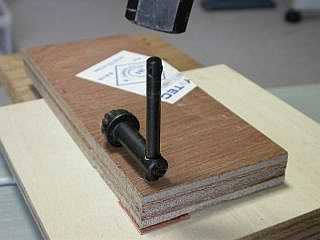 |
|
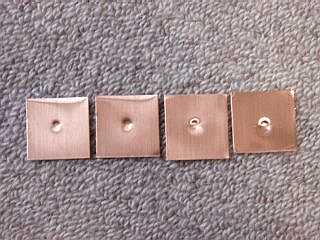 |
|
|
板にチャックハンドル横棒が通る穴をあけ、その板と別な板の間に銅板を挟み、玄翁で横棒を叩き凹みをつけます。
|
|
凹ましが終わった銅板。 左の工程で板と板の間に挟むのは銅板全体が歪まないようにという配慮です。
|
|
|
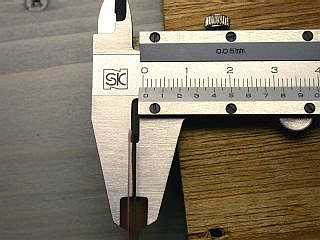 |
|
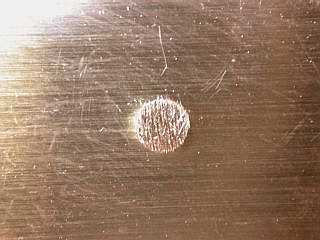 |
|
|
ノギスで厚みの増加を測り出っ張り量が0.3-0.4mmにします。 この例では0.7mmですので、0.4mm出っ張っていることになります。
|
|
出っ張った部分を中目のヤスリで削りますが、厚みの変化をノギスで確認しながら0.25mm削ります。 (計算上凹みの中央部の厚みが0.05mmとなります。)
|
|
|
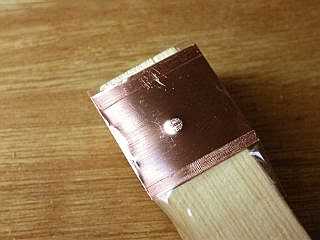 |
|
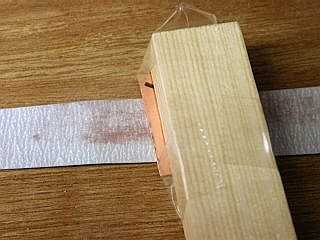 |
|
|
銅板の凸面を上にして木の棒にセロファンテープで貼り付けます。
|
|
#600のサンドペーパーで研磨し面を平らにします。 これで凹み中央の厚みは0.03-0.05mmとなります。 (ノギスの測定限界は0.05mmですが、で0.05mm以下になっているかどうかは確認できます。)
|
|
|
 |
|
 |
|
|
#600ペーパーによる研磨が完了したところです。
|
|
割り箸にホッチキスで針を打ち込みこれを抜いた穴に針をペンチでくわえ刺し込みます。 (私は一寸法師の剣だと言っています?!)
|
|
|
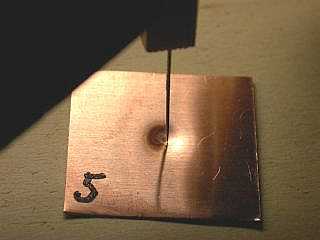 |
|
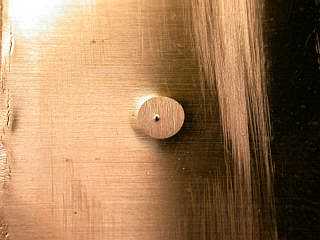 |
|
|
銅板凸面を平らな板の上に置き針で穴をあけますが、刺さったなと感じたらそこで止め反対側に0.7mm針先が出ていることをノギスで確認します。 (凹み面からだと0.75mm近く刺さったことになります。)
|
|
凸面の穴の周りにはこのようにバリが出ますので、#600ペーパーで削り落とします。 (この時板の厚みが若干薄くなり穴径もほんの少し大きくなります。) |
|
|
#600のペーパーでバリを落としたら針を凹面側から穴に挿して回転させ真円になるよう軽く成形します。
次に高倍率ルーペで凸面側の穴の周りを見てバリがないかどうか確認します。 バリがあったらまた#600で研磨して落
とし針で真円成形を繰り返します。
(注意:針で真円成形する際穴径は大きくなりますから、押す力を掛けすぎないよう。 それでも真円成形が終わる頃に
は針が0.9-1.0mm刺さる状態となり、穴径は0.2mm前後の所定の径になります。)
また銅板を明るい方にかざし斜め方向からピンホールを見て穴を通る光が見えなくなる角度をチェックします。
その角度が12度以下になれば穴の周りの板厚は0.043mm以下となりまずまずの薄さとなります。 これよりも大きい 角度で光が見えなくなったら肉厚が厚すぎますので、銅板凸面を#600で更に研磨する必要があります。
その場合には真円成形もやり直さなければなりません。
最後に高倍率ル-ぺでもう一度真円となっていることを確認したら終了です。
|
|
|
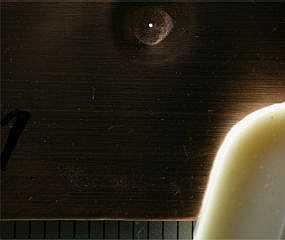 |
|
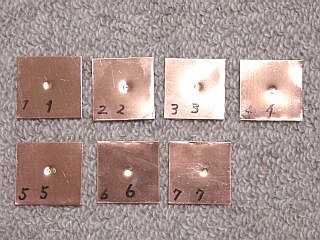 |
|
|
ピンホール板をノギスに貼り明るい方向に向けながら、ノギスの目盛りを含めデジカメで接写しました。 PC画面上の拡大測定で直径約0.21mm、ほぼ真円でした。 (1704x2272の拡大画面をこちらからご覧いただけます。)
|
|
完成した7枚のピンホール板。 とはいってもこの大きさではピンホールの様子は判るわけありませんが、左写真の測定法によるとピンホール直径は0.19mmから0.22mmの間に入っています。
|
|
|
左上の写真ファイルをパソコン画面で拡大してみれば真円具合や直径が測定できます。
私は良い物を選別するため一度に7枚作りましたが、こうして測ったピンホール直径は、0.19-0.22mmの間でした。
真円度は何れも良さそうで、ピンホール周りの板厚は0.035-0.045mmの間で7枚何れも使い物になりそうです。
|
|